Disulfide bond and free radical copolymerization endow TPU with reversible cross-linking properties
Wenxin Gan, Hanyu Xue, Hongyi Lin, Renjin Gao, Yuchi Zhang, Liwei Wang, Jiuping Rao
Vol. 19., No.3., Pages 311-325, 2025
DOI: 10.3144/expresspolymlett.2025.22
DOI: 10.3144/expresspolymlett.2025.22
GRAPHICAL ABSTRACT
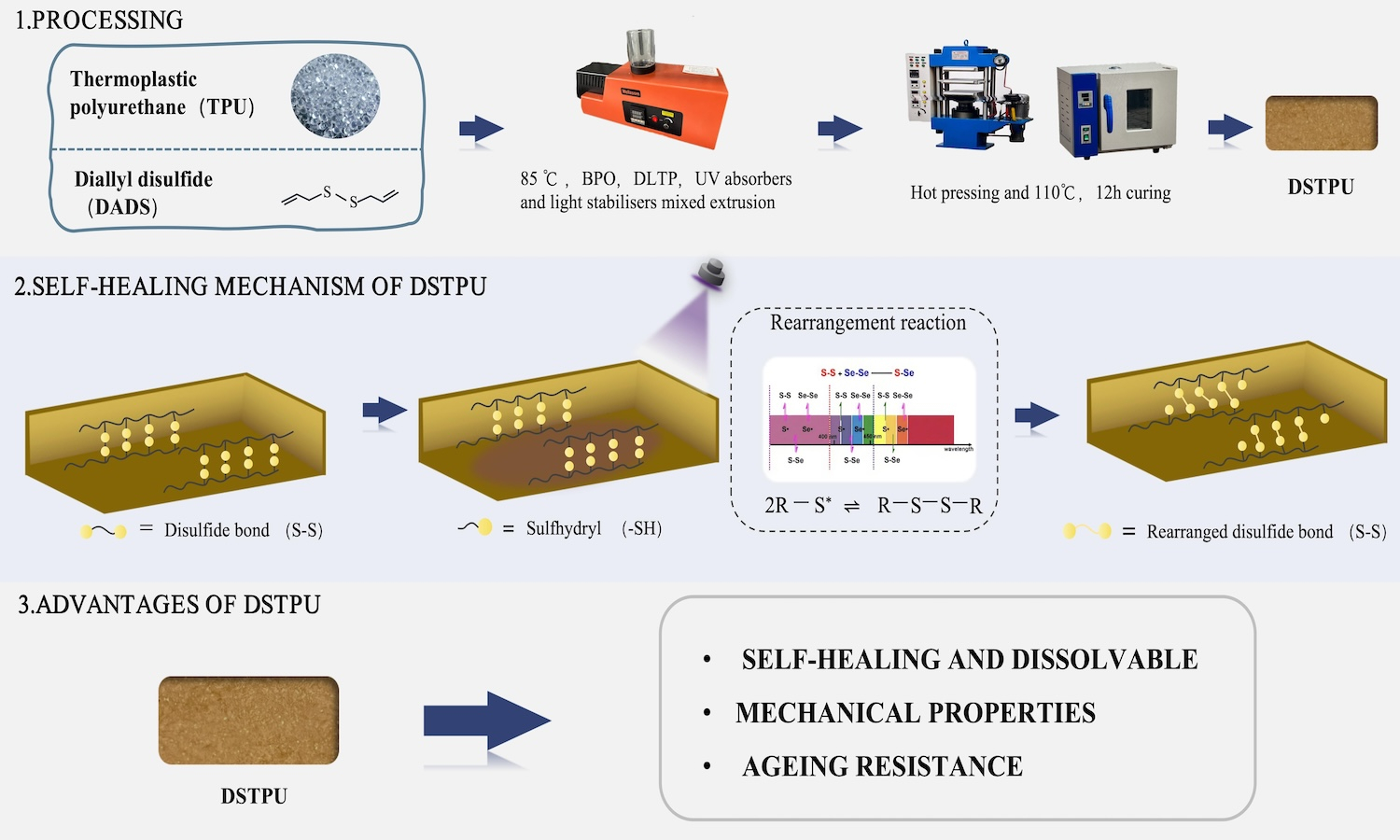
ABSTRACT
Cross-linking frequently enhanced the mechanical properties of linear polymeric materials; however, it also resulted in the transition from thermoplastic to thermosetting materials, which posed issues from an environmental perspective. Thermoplastic polyurethane (TPU) elastomers were extensively applied across various industries. To improve the mechanical properties of TPU while preserving its environmental benefits, this study integrated radical copolymerization technology to develop a reversible crosslinked TPU. Specifically, the linear polyurethane molecular chains were crosslinked using diallyl disulfide (DADS) as a functional cross-linking monomer. Through radical copolymerization reactions, reversible crosslinks formed from disulfide bonds were created between the linear polyurethane molecular chains, yielding a self-healing reversible crosslinked thermoplastic polyurethane (DSTPU). The study showed that DSTPU could self-heal and dissolve under UV light and alkaline N,N-dimethylformamide (DMF) conditions, achieving 82.2% self-healing efficiency at 3 phr DADS. It dissolved into fine particles in alkaline DMF. Disulfide bonds in DSTPU enhanced cross-linking, boosting 19% oxygen permeability, thermal conductivity (0.218 W/(m·K)), and mechanical properties like tensile stress (11.18 MPa), force (134.13 N), and elongation (548%). These bonds also enhanced aging resistance, cutting ΔYI to 6.0%.
RELATED ARTICLES
Dániel Gere, Tamás Bárány
Vol. 19., No.6., Pages 554-555, 2025
DOI: 10.3144/expresspolymlett.2025.41
Vol. 19., No.6., Pages 554-555, 2025
DOI: 10.3144/expresspolymlett.2025.41
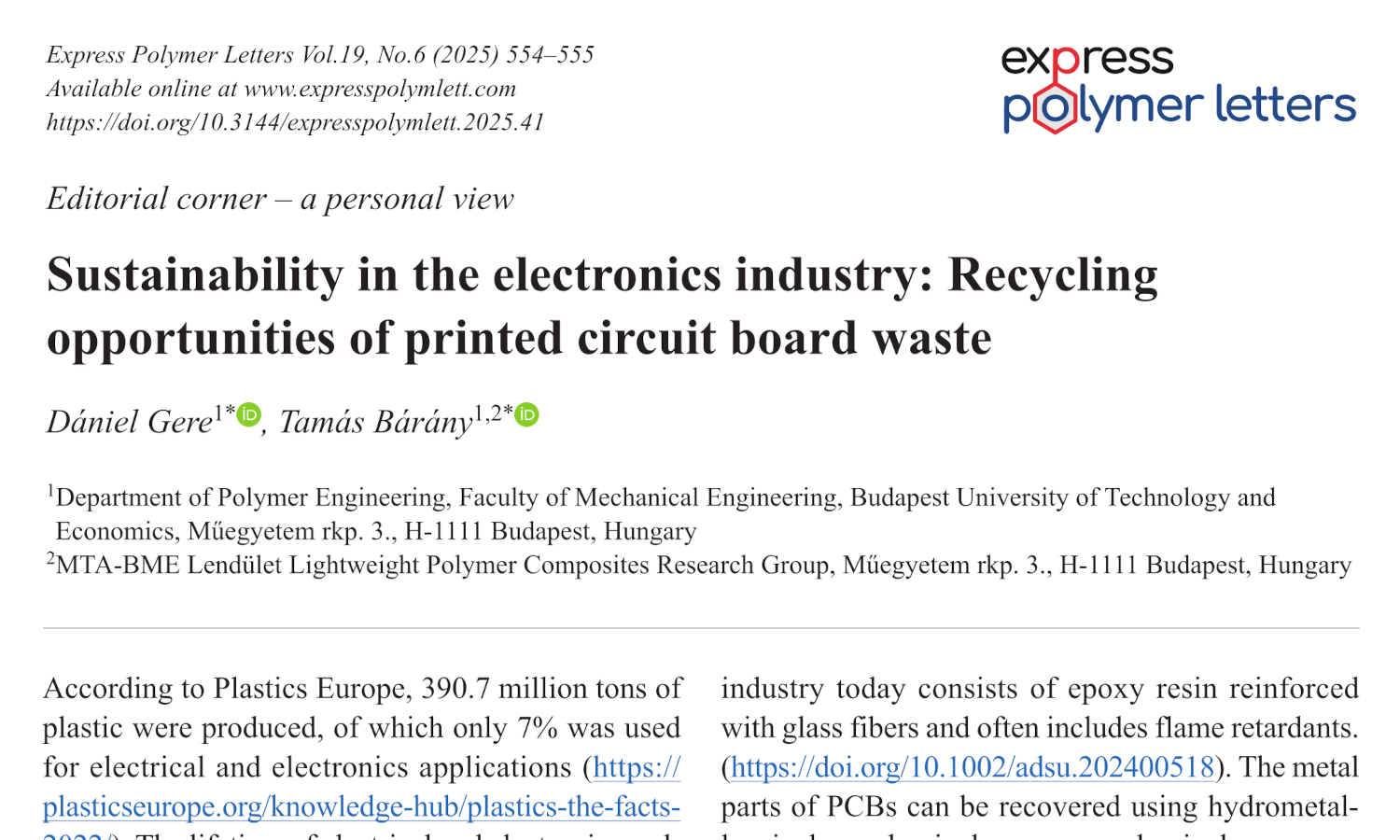
This is an editorial article. It has no abstract.
Andrea Toldy
Vol. 19., No.4., Pages 350-350, 2025
DOI: 10.3144/expresspolymlett.2025.25
Vol. 19., No.4., Pages 350-350, 2025
DOI: 10.3144/expresspolymlett.2025.25
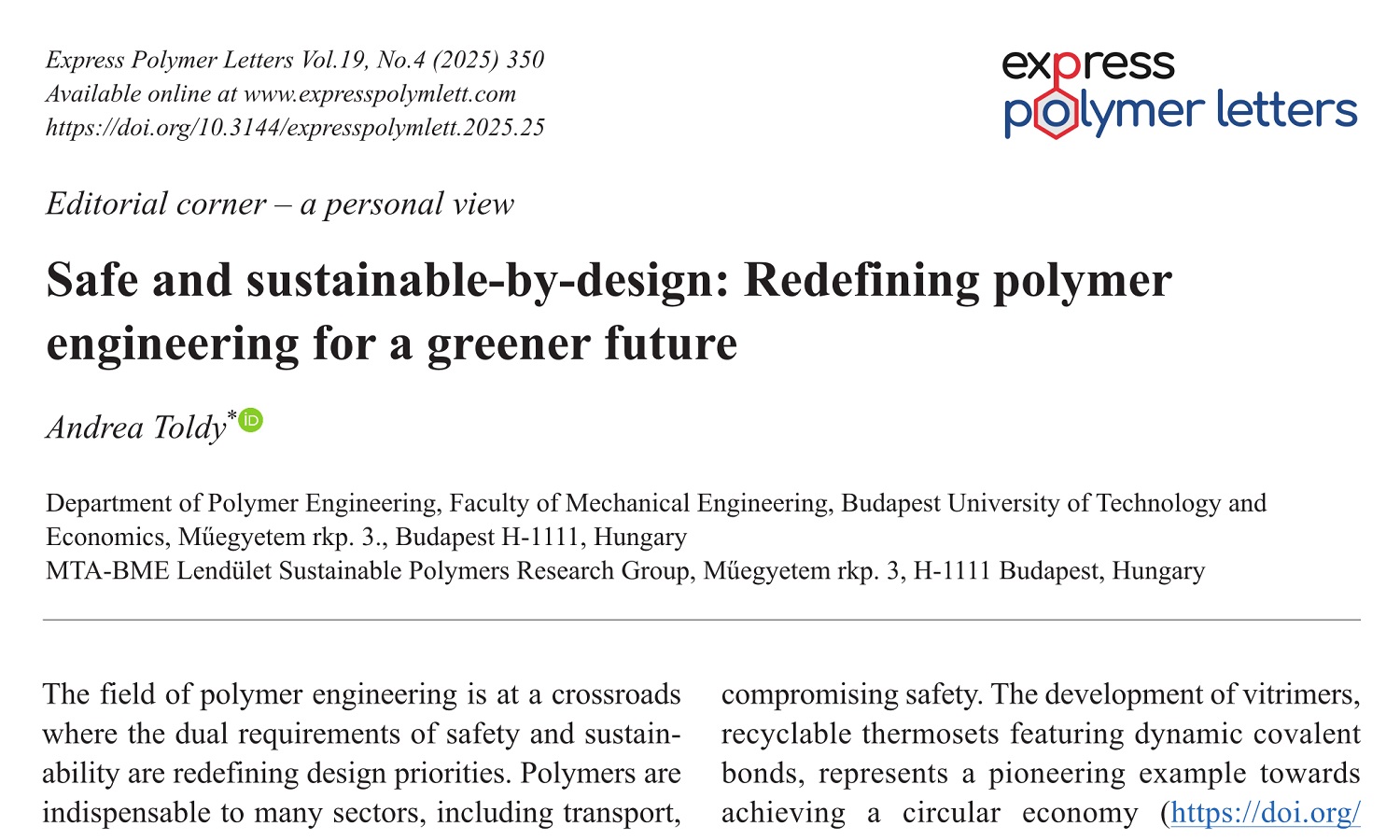
This is an editorial article. It has no abstract.
Zaheer ul Haq, Teng Ren, Xinyan Yue, Krzysztof Formela, Denis Rodrigue, Xavier Colom Fajula, Tony McNally, Dong Dawei, Yong Zhang, Shifeng Wang
Vol. 19., No.3., Pages 258-293, 2025
DOI: 10.3144/expresspolymlett.2025.20
Vol. 19., No.3., Pages 258-293, 2025
DOI: 10.3144/expresspolymlett.2025.20
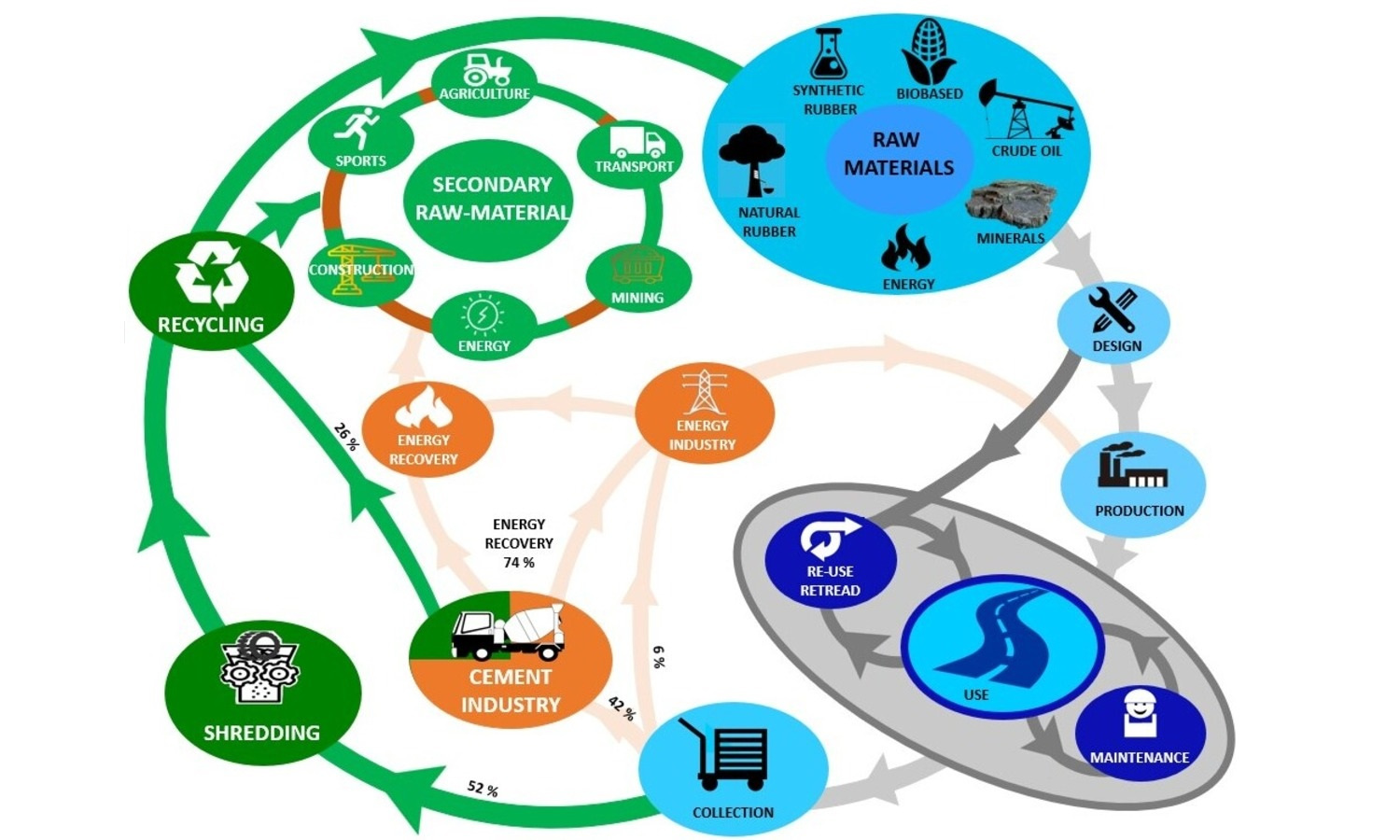
As a complex composite material, tire rubber has always presented significant environmental and waste management concerns due to its non-biodegradability and accumulation in landfills. The devulcanization of tire rubber has emerged as a historical challenge in the field of sustainable rubber engineering since Goodyear invented cross-linking in 1839. This review provides a comprehensive analysis of waste tire recycling processes, focusing on the sources, legislation, management strategies, and utilization across different regions. It explores the multifaceted challenges of devulcanizing rubber, with a specific focus on transitioning from ground tire rubber to the concept of multi-decrosslinking: sulfur bridge breakage, rubber chain depolymerization and micro-nano sized core-shell carbon black. Ideal devulcanization has restricted the release of reinforcing fillers, resulting in devulcanized rubber mainly containing dozens of micron particles, which hinder the wide usage of devulcanized rubber. This review comprehensively assesses the current state-of-the-art techniques for tire rubber devulcanization, including physical, chemical and biological methods. It explores the intricacies of ground tire rubber as a starting material, structural evolution of ground tire rubber during the devulcanization process and the associated challenges in achieving efficient devulcanization while retaining desirable mechanical properties. Furthermore, through an in-depth analysis of recent advancements, limitations and prospects, this paper offers a complete understanding of the challenges faced in tire rubber devulcanization. Considering the technical and environmental aspects of these processes, this work contributes to multi-decrosslinking, the ongoing discourse on sustainable materials development and circular economy initiatives, which pave the way for future innovations in the field of rubber recycling.
Shengao Yang, Yan Wang, Fang Wang, Kaiyi Zhang, Xinxin Lv, Hao Teng, Rui Zheng, Faliang Luo, Qian Xing
Vol. 19., No.1., Pages 94-106, 2025
DOI: 10.3144/expresspolymlett.2025.7
Vol. 19., No.1., Pages 94-106, 2025
DOI: 10.3144/expresspolymlett.2025.7
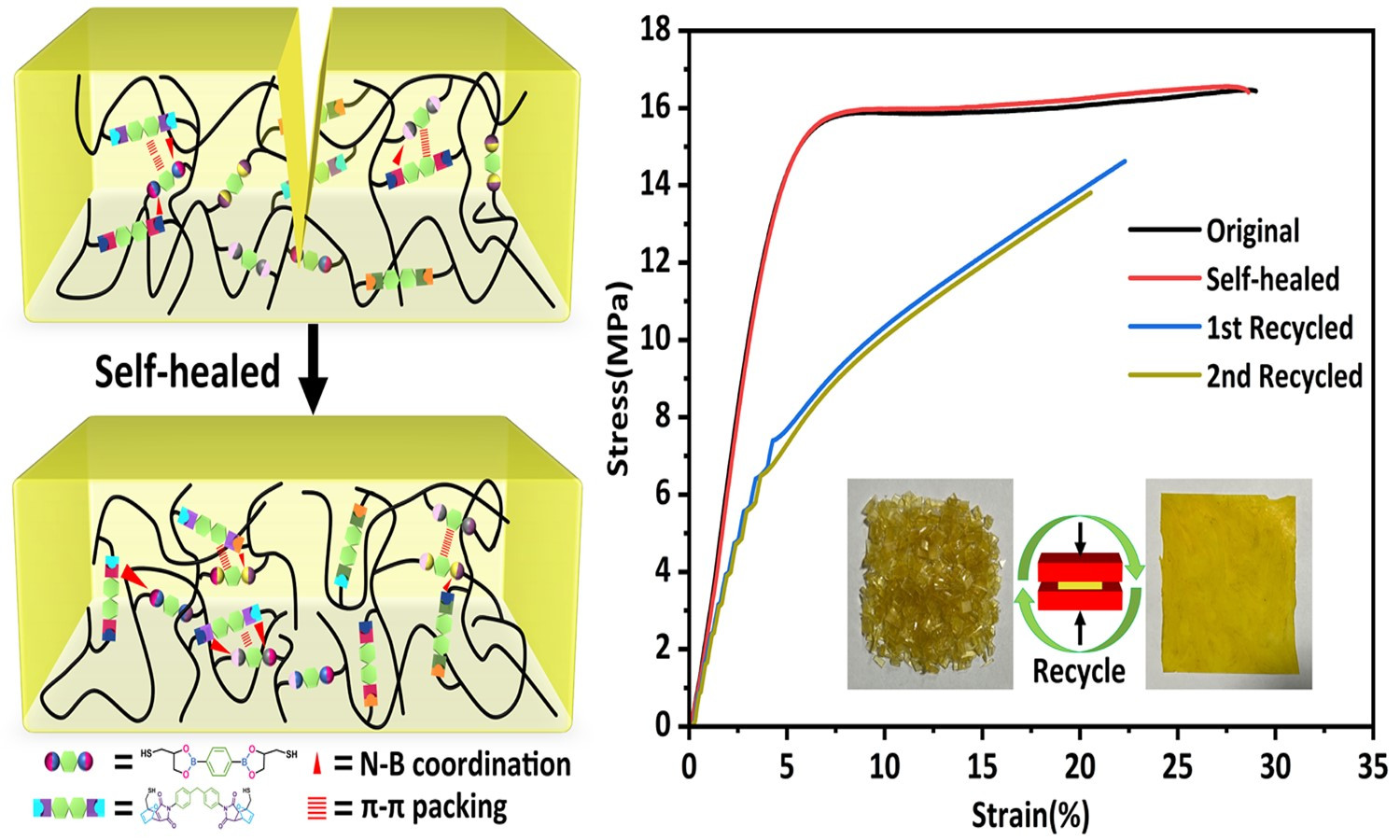
Dynamic cross-linked networks (DCNs) endow thermoset rubber with self-healability and recyclability to extend its lifetime and alleviate environmental pollution. However, the contradiction between high self-healing and mechanical properties in DCNs rubber is always difficult to be resolved. Herein, we used boronic ester (BO) and Diels-Alder dynamic covalent bonds (DA) to synthesize polybutadiene-based dual networks rubber (PB-BO-DA) via thiol-ene reaction. This approach achieved a tensile strength of 16.46 MPa and 99% self-healing efficiency, facilitated by extensive intermolecular interactions (π-π packing and N-B coordination) and fully dynamic cross-linking. In addition, multiple dynamic cross-linked networks (MDCNs) polybutadiene-based rubber also show excellent shape memory ability and recyclability. This strategy might open a helpful pathway to fabricate intelligent multifunctional polymers with high strength and high self-healing efficiency.
Ming Qiu Zhang
Vol. 18., No.6., Pages 559-560, 2024
DOI: 10.3144/expresspolymlett.2024.41
Vol. 18., No.6., Pages 559-560, 2024
DOI: 10.3144/expresspolymlett.2024.41
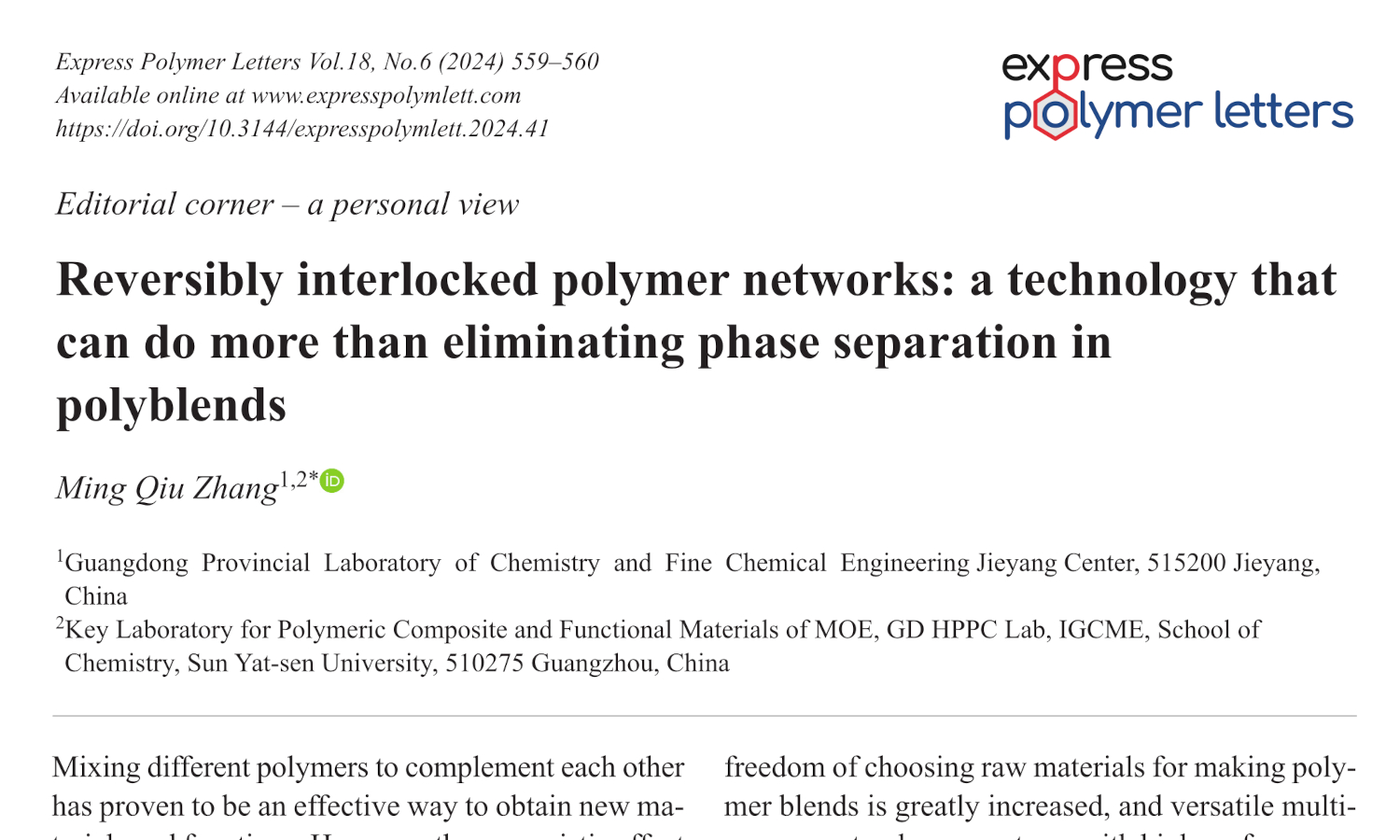
This is an editorial article. It has no abstract.