Removal of arsenic (III) and (V) from water bodies by using biopolymers via adsorption: A review
Warda Masoom, Ayesha Khan, Amna Sarwar, Sara Musaddiq, Zahoor Hussain Farooqi, Sadia Iqbal
Vol. 18., No.3., Pages 260-281, 2024
DOI: 10.3144/expresspolymlett.2024.19
DOI: 10.3144/expresspolymlett.2024.19
GRAPHICAL ABSTRACT
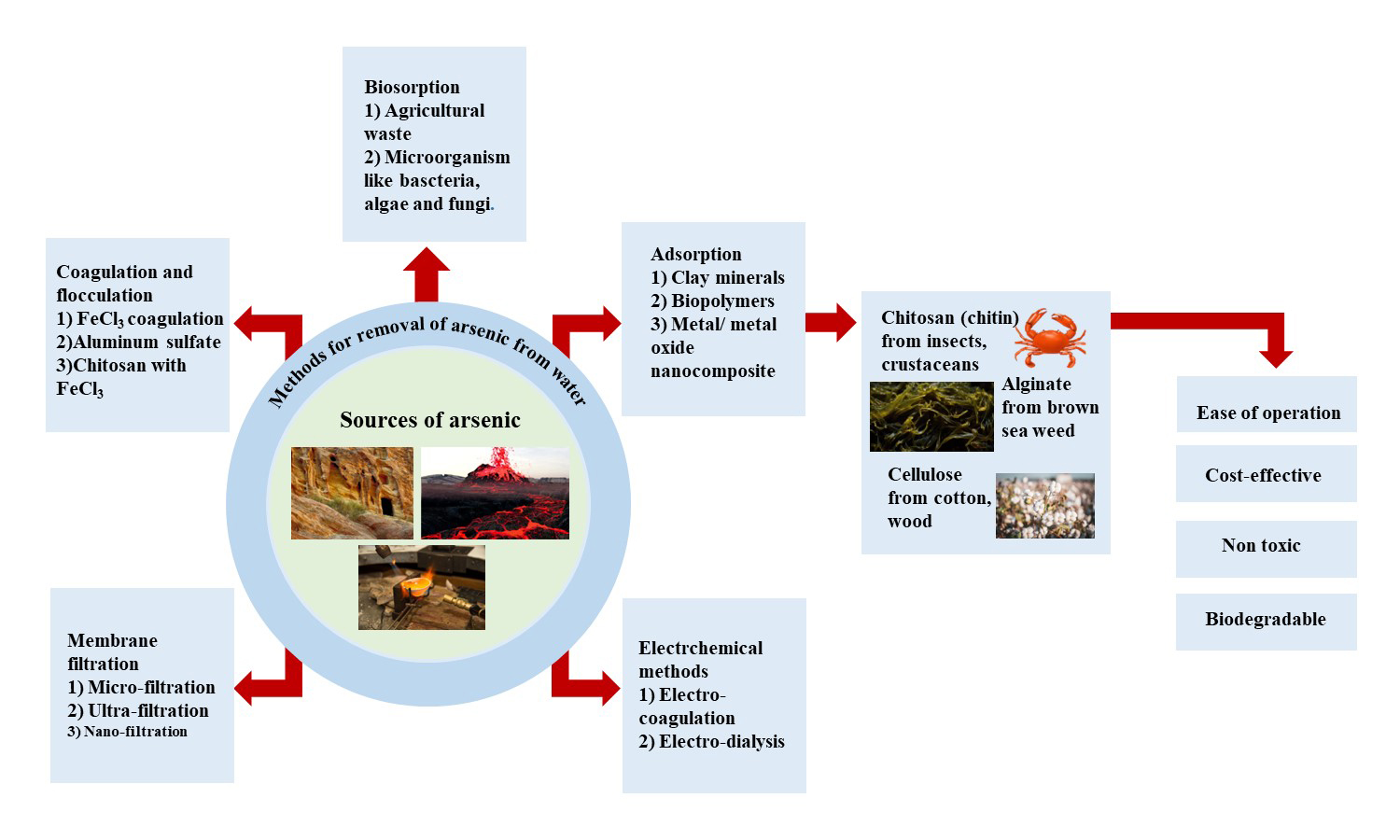
ABSTRACT
Arsenic, an element found in the Earth’s mantle, can be highly toxic, especially in its As (III) form. It enters our food chain through human activities like melting metals, using arsenic-based pesticides, and natural processes like volcanoes and rock breakdown. Consuming too much arsenic is extremely dangerous, impacting many countries worldwide. To tackle this issue, various methods like filtering, adding chemicals, and using electricity have been developed to clean arsenic-contaminated water. Among these, adsorption is a standout approach due to its simplicity and effectiveness. Biopolymers from living sources offer a natural solution, easily tweaked for arsenic removal. These biopolymers contain functionalities that can strongly latch onto toxic materials, acting like magnets. By customizing them with compounds like titanium dioxide (TiO2), magnetite (Fe3O4), and others, they become even better at capturing arsenic, shaped into tiny particles or beads. This adaptation makes biopolymers a promising choice for cleaning arsenic from water. This review focuses on ways to clean water, specifically exploring how materials like chitosan, alginate, and modified cellulose can be used to remove arsenic by adsorption. It investigates how these materials work under different conditions, highlighting important details. By sharing these insights, this article contributes to the ongoing efforts to ensure cleaner water resources.
RELATED ARTICLES
Guilherme Ribeiro de Carvalho, Rafael Affonso Netto, Camila Delarmelina, Marta Cristina Teixeira Duarte, Liliane Maria Ferrareso Lona
Vol. 19., No.7., Pages 686-696, 2025
DOI: 10.3144/expresspolymlett.2025.52
Vol. 19., No.7., Pages 686-696, 2025
DOI: 10.3144/expresspolymlett.2025.52
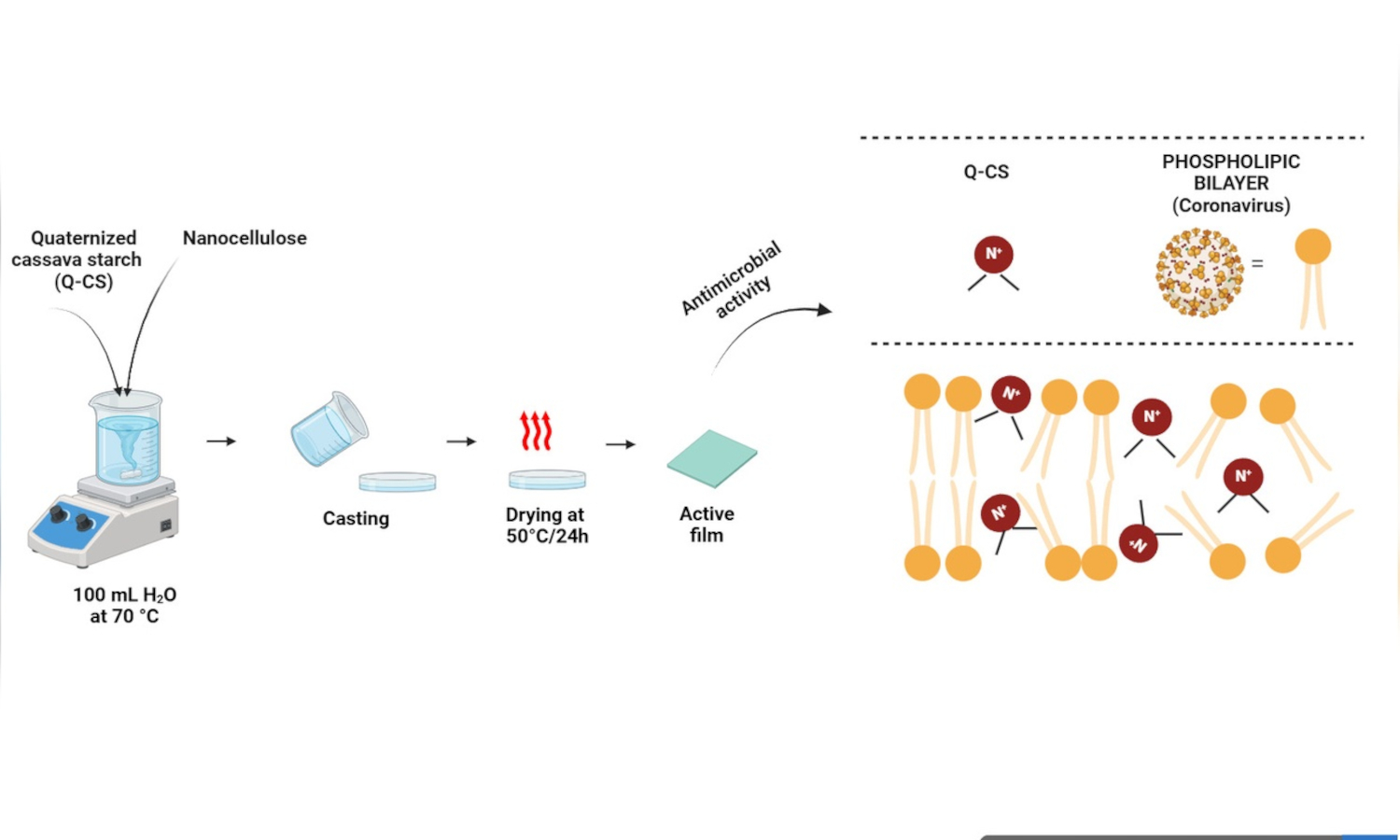
In this study, a new plastic film with antiviral and antibacterial properties was developed using modified cassava starch with glycidyltrimethylammonium chloride (GTMAC) and reinforced by crystalline nanocellulose (CNC), called Q-CS/CNC. For comparison, a control film (Q-CS) was produced without the addition of CNC. Elemental analysis revealed a degree of substitution (DS) of 0.552, indicating the replacement of the OH groups of starch by the NR4+ groups of GTMAC during the quaternization reaction. The addition of CNC resulted in significant increases (p < 0.05) of 38.9, 38.2, and 43.1% in thickness, opacity, and water vapor permeability measurements, respectively, compared to Q-CS. Incorporating CNC also contributed to an increase of 43.6% in tensile strength and 109% in stiffness but slightly decreased thermal stability. The Q-CS/CNC film demonstrated efficacy by inactivating 99% of the coronavirus in 1 min and inhibiting the growth of Staphylococcus aureus and Escherichia coli. This action is attributed to the electrostatic interaction of quaternary amino groups, grafted onto starch, with the phospholipid membrane of microorganisms, resulting in the inactivation of these microorganisms. Therefore, these results highlight the potential use of Q-CS/CNC film as antimicrobial packaging, especially against coronavirus.
Lilla Bubenkó, Násfa Németh, Sára Frey, Tamás Molnár, Károly Belina, Orsolya Viktória Semperger
Vol. 19., No.7., Pages 726-735, 2025
DOI: 10.3144/expresspolymlett.2025.55
Vol. 19., No.7., Pages 726-735, 2025
DOI: 10.3144/expresspolymlett.2025.55
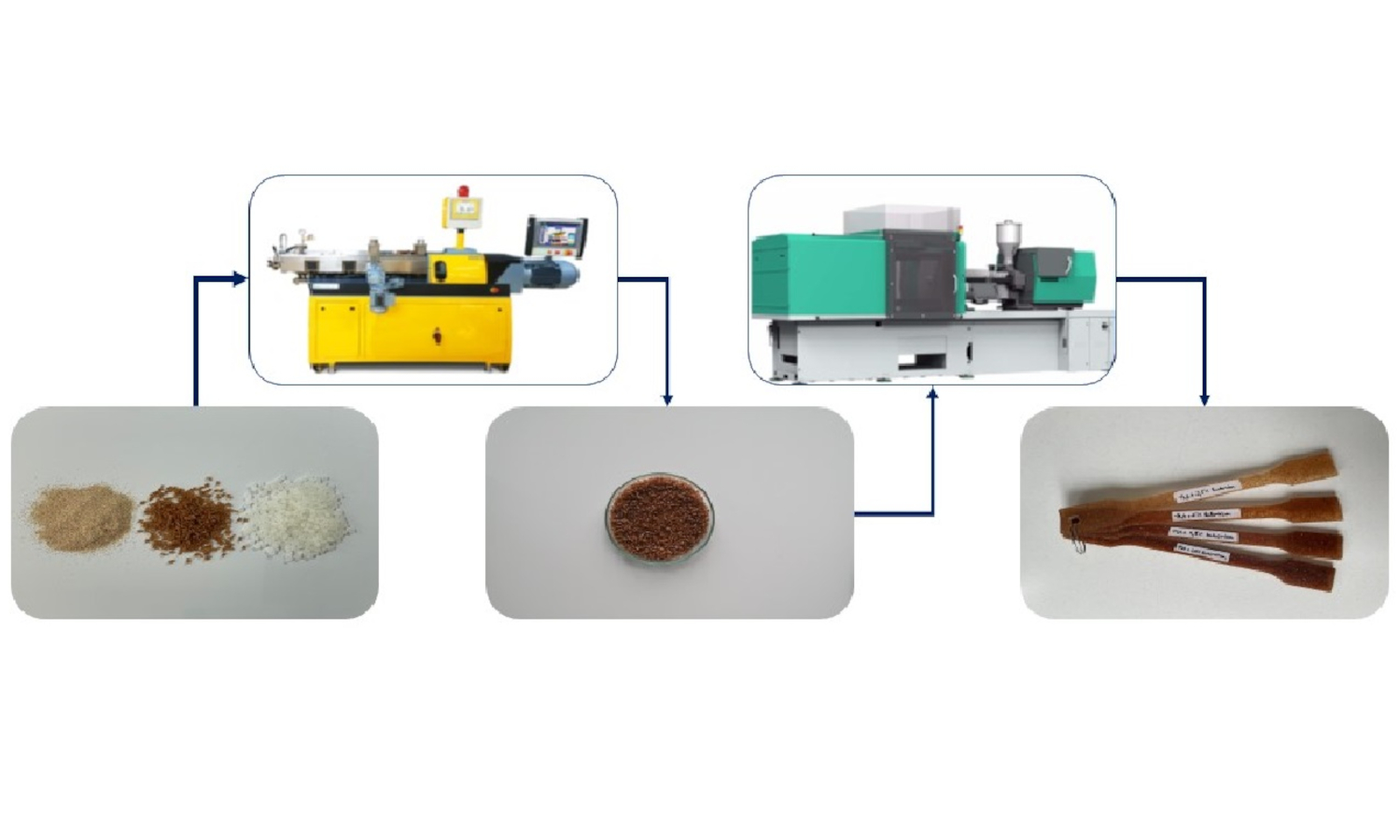
Biocomposites have recently received more attention because of raising environmental awareness and the drive toward sustainable technologies. The most common biodegradable polymer is poly(lactic acid) (PLA), which has an excellent balance of physical and rheological properties, but there is some limit to its usage. PLA properties can be improved by adding different types of fibers or fillers that come from agricultural waste. In this study, corn cob and lavender stem were used to reinforce PLA without any coupling agent, and the properties of the composites were investigated. The melt flow rate (MFR) values decreased with the corn cob content and increased with the addition of lavender stem. Mechanical tests showed that the tensile and flexural modulus of the composites increased and the strengths decreased with the reinforcement material content. The rigidness of PLA slightly decreased with the addition of fillers. There was no significant effect on the thermal properties. The unremarkable improvement of the reinforcement was due to the lack of appropriate adhesion of the two phases. The structure of the compounds was found to be homogenous on the scanning electron microscopy (SEM) micrographs. The incorporation of corn cob and lavender stem can reduce the production cost of materials.
Seisuke Ata, Takumi Ono, Motonari Shibakami
Vol. 19., No.6., Pages 628-635, 2025
DOI: 10.3144/expresspolymlett.2025.47
Vol. 19., No.6., Pages 628-635, 2025
DOI: 10.3144/expresspolymlett.2025.47
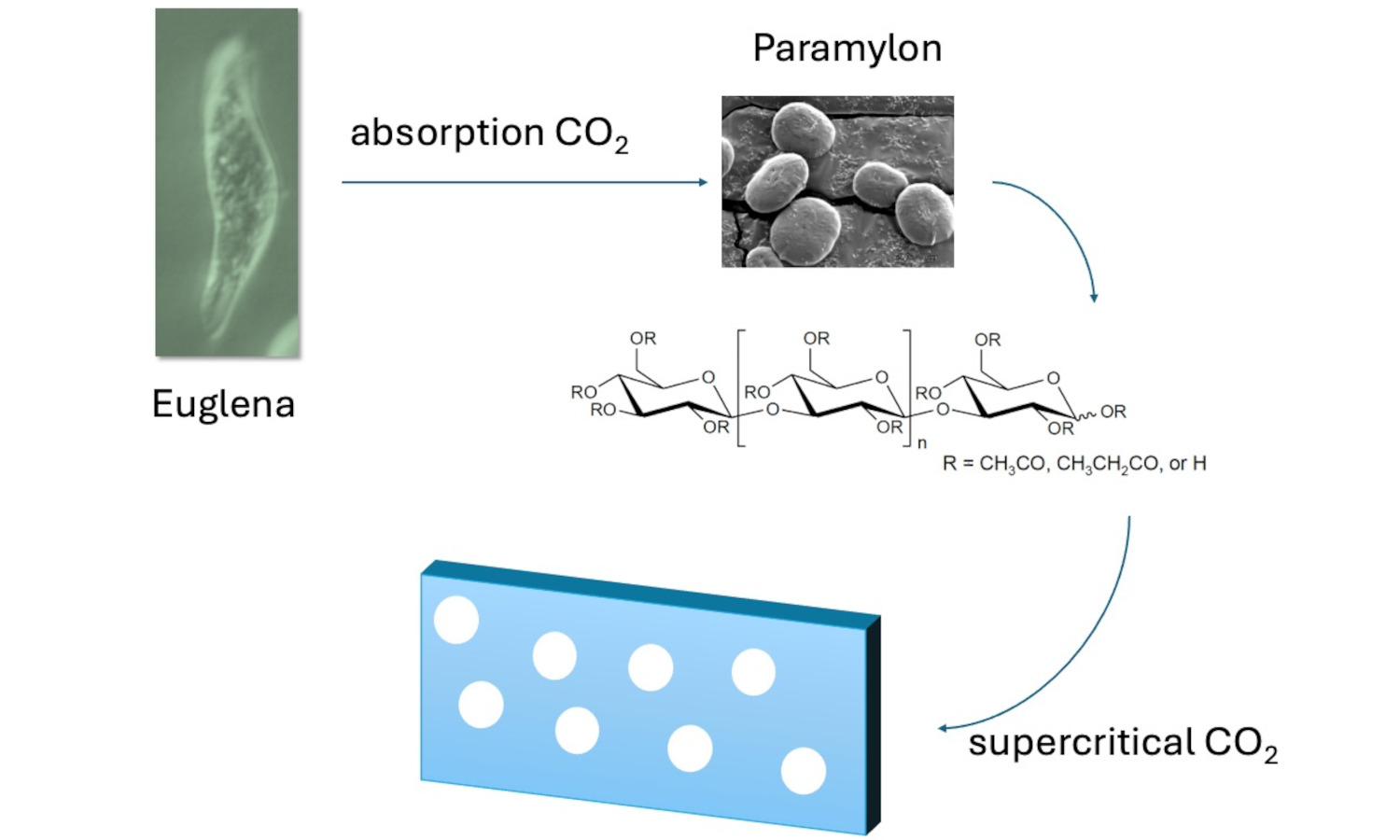
This study demonstrated, for the first time, the successful formation of porous paramylon esters, which were made from euglenoid polysaccharide known as paramylon and short-chain fatty acids, through supercritical CO2 processing. By maintaining a constant ester functional group attached to the paramylon and varying its proportion, distinct porous structures were selectively produced. Solubility parameter estimations indicated that changes in esterification had no significant effect on the solubility of the paramylon esters used in the experiment. Thus, these structural differences are likely attributed to variations in the viscoelastic properties of paramylon esters under supercritical CO2 conditions. Furthermore, thermal conductivity measurements revealed reductions of up to 20%. Intriguingly, substantial decreases in thermal conductivity were observed even at low foaming ratios, achieved through precise control of the porous structure.
Katalin Litauszki, Tamás Tábi, László Mészáros
Vol. 19., No.5., Pages 455-456, 2025
DOI: 10.3144/expresspolymlett.2025.33
Vol. 19., No.5., Pages 455-456, 2025
DOI: 10.3144/expresspolymlett.2025.33
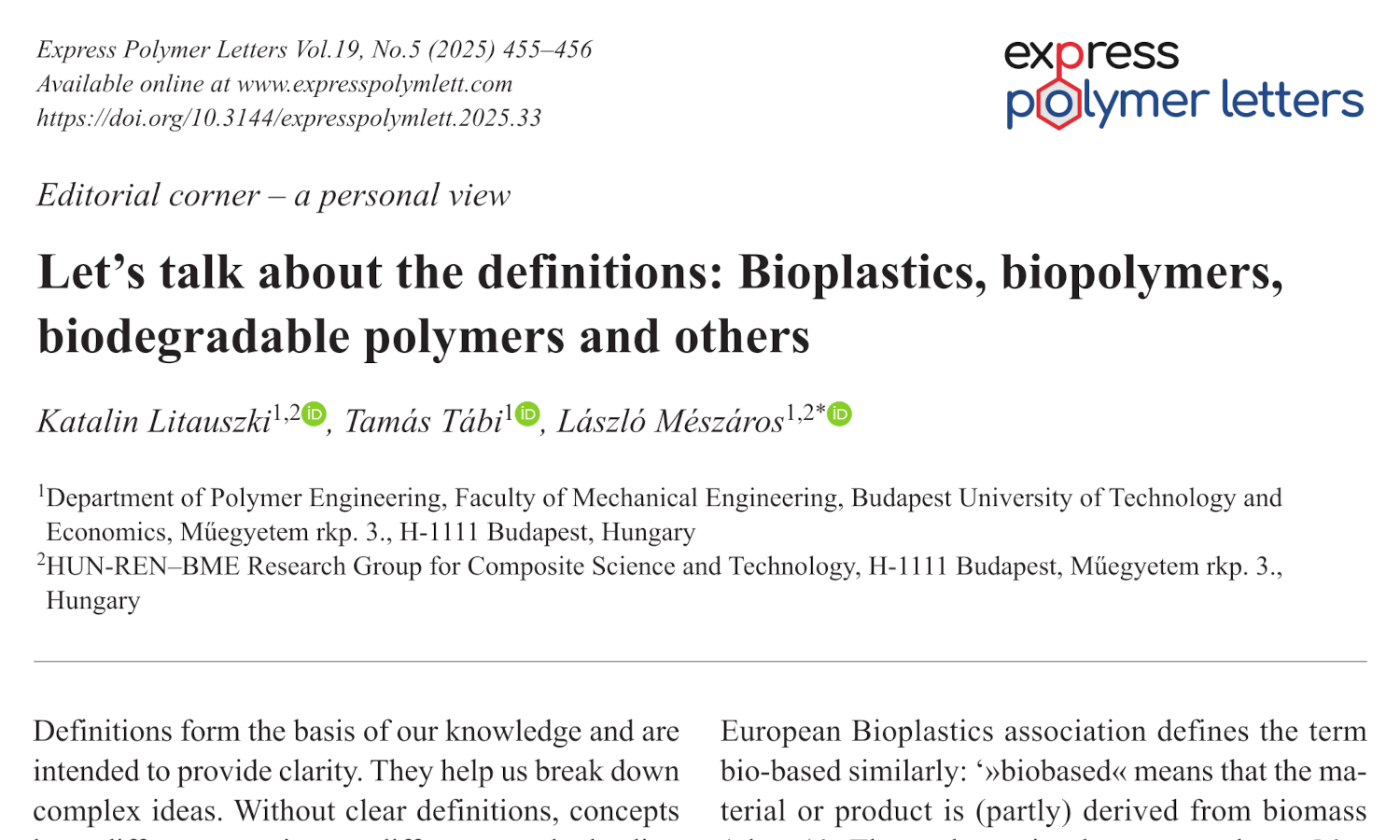
This is an editorial article. It has no abstract.
Sarahí Bautista Reberte, Esmeralda Zuñiga Aguilar, Solange Ivette Rivera Manrique, Carlos Alberto Martínez-Pérez
Vol. 19., No.3., Pages 326-338, 2025
DOI: 10.3144/expresspolymlett.2025.23
Vol. 19., No.3., Pages 326-338, 2025
DOI: 10.3144/expresspolymlett.2025.23
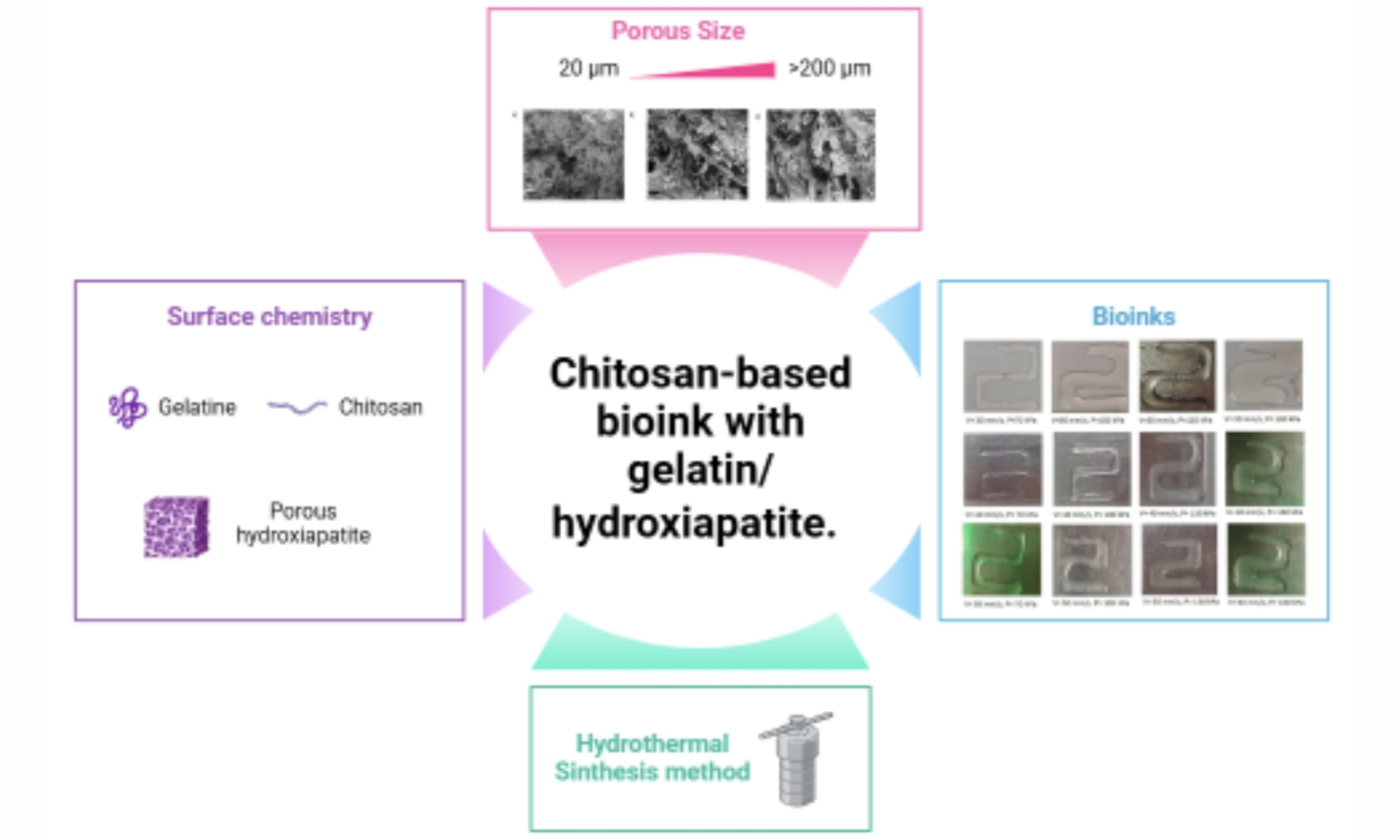
Three-dimensional (3D) bioprinting is a technique currently used for creating tissue engineering scaffolds, using bioinks as the building blocks. These bioinks are composed of biomaterials that provide structural integrity and are synthesized from organic polymers to enhance biocompatibility with the printed constructs. In this study, a series of eleven chitosan-based bioinks were synthesized using the sol-gel technique, employing chitosan of low and medium molecular weight. Three bioink formulations were selected based on their viscosity characteristics and further enriched with gelatin and hydroxyapatite (HA) to enhance their mechanical properties. Characterization tests included Fourier-transform infrared spectroscopy (FTIR), thermogravimetric analysis (TGA), scanning electron microscopy (SEM), and rheological assessments. Viscoelastic materials were obtained, and an experimental model was developed to optimize printing parameters, focusing on pressure and printing speed. Our findings indicate that a bioink formulation comprising a blend of medium and high molecular weight chitosan, supplemented with gelatin and hydroxyapatite, was found to be a promising approach for fabricating scaffolds for bone tissue repair.