Determination of wall thickness effect of in-mold viscosity measurement under non-adiabatic, non-isothermal flow conditions
Vol. 19., No.3., Pages 246-257, 2025
DOI: 10.3144/expresspolymlett.2025.19
DOI: 10.3144/expresspolymlett.2025.19
GRAPHICAL ABSTRACT
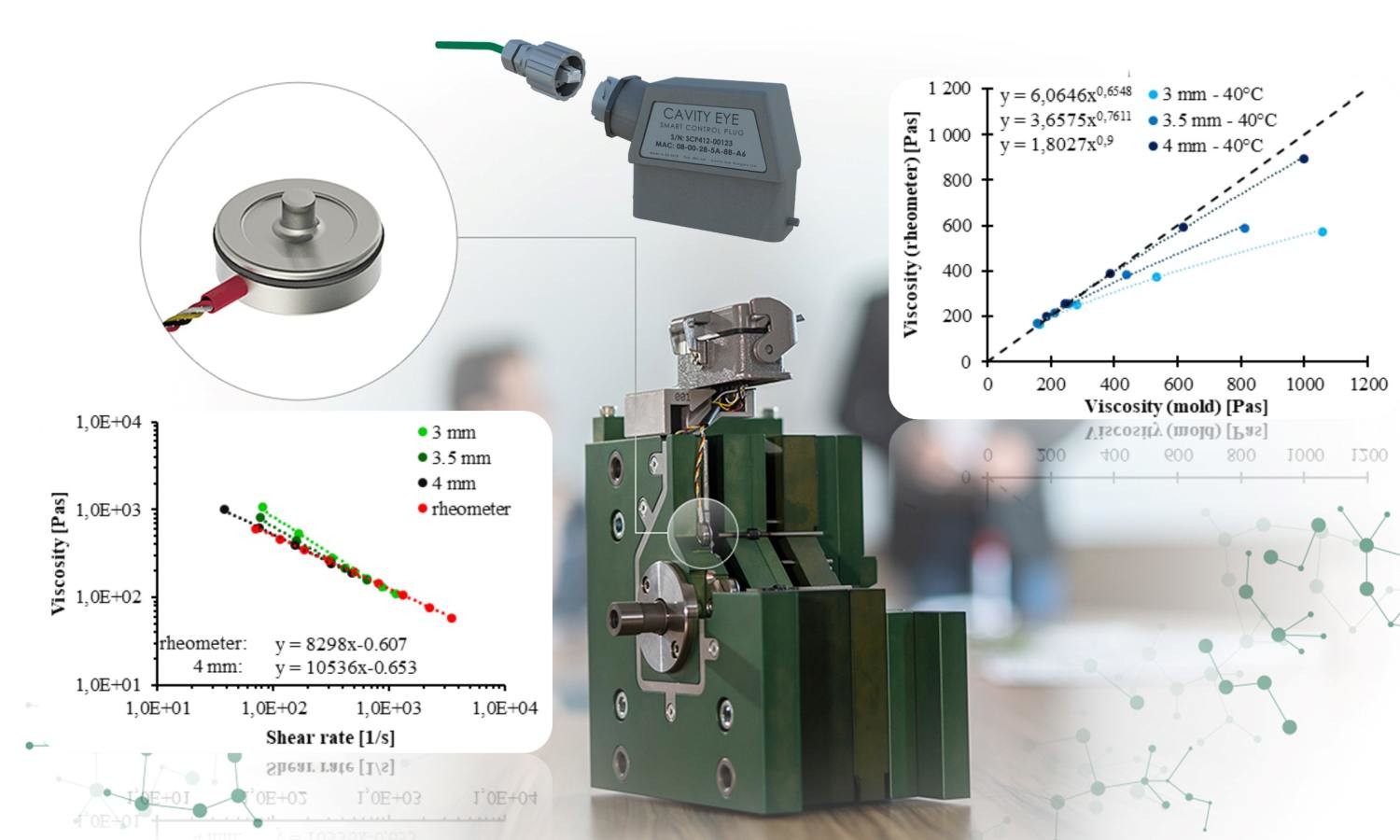
ABSTRACT
Measuring the viscosity of the melt contributes to the quality of injection molded products. Injection molding machines cannot give much feedback on the processes in the cavity, so pressure measurement inside the mold facilitates quality supervision. Our goal is to get more information about the viscosity of the material during filling in a traditional injection mold. A suitable and cost-effective method is to install cavity pressure sensors for the in-situ viscosity measurement. We prepared an experimental mold with variable wall thickness and 80×80 mm cavity dimensions. We implemented eight pressure sensors in each cavity. The wall thickness varied from 1 to 4 mm, and apparent viscosity was determined at different shear rates and mold temperatures. We measured non-isothermal and non-adiabatic flow during filling. The environment was quite different from that of standard measuring equipment. Based on the results, we effectively measured the material viscosity with a non-heated mold in the case of acrylonitrile-butadiene-styrene (ABS) and polypropylene (PP) material. The results were validated by measuring viscosity with a capillary rheometer and compared to our method using the non-heated mold, and the error was less than 10%. The results were accurate in a specific speed wall thickness range with PP and ABS.