Improving the mechanical properties of fiber-reinforced polymer composites through nanocellulose-modified epoxy matrix
Vol. 18., No.1., Pages 61-71, 2024
DOI: 10.3144/expresspolymlett.2024.5
DOI: 10.3144/expresspolymlett.2024.5
GRAPHICAL ABSTRACT
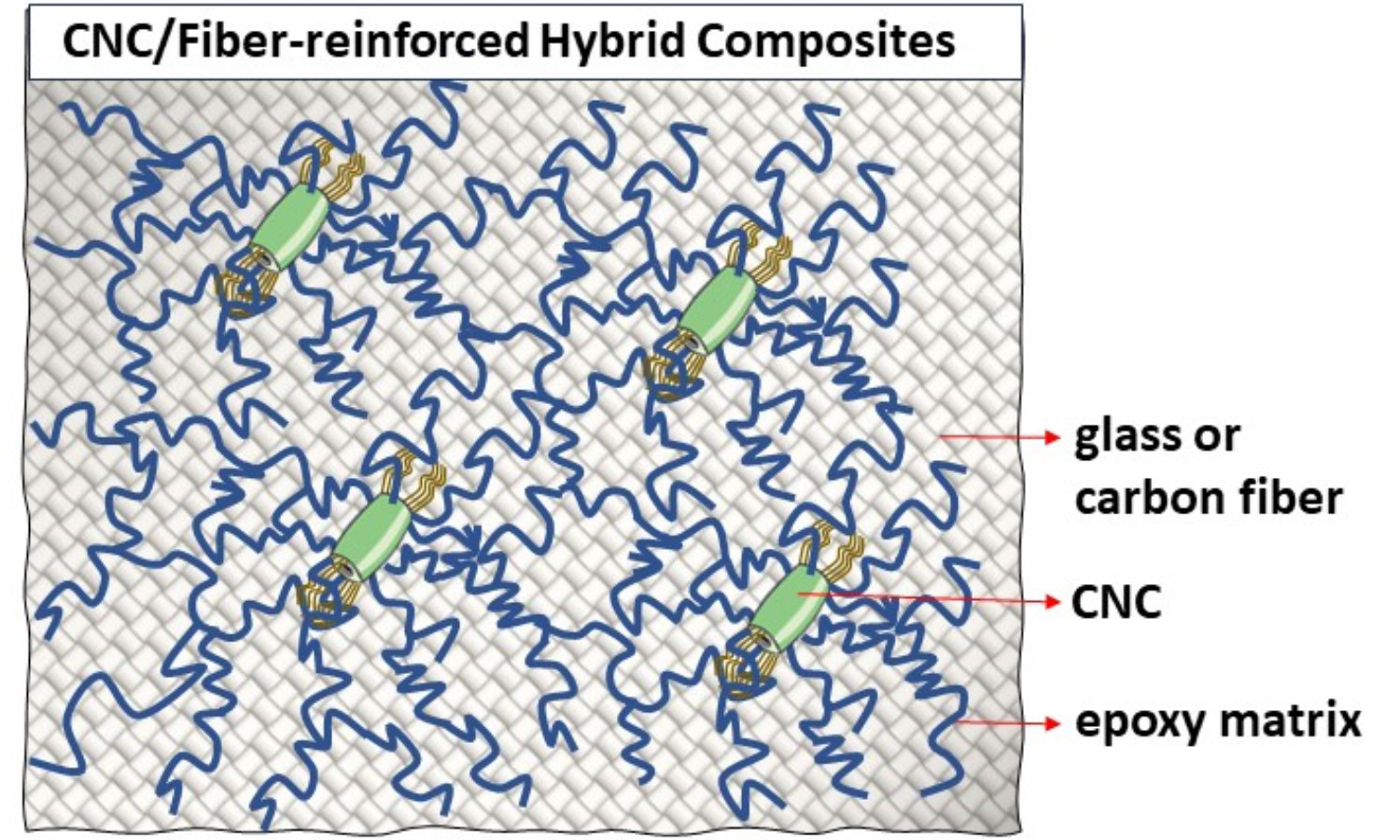
ABSTRACT
In this study, the potential use of nanocrystalline cellulose (CNC) modified epoxy nanocomposite as a matrix is investigated for both glass and carbon fiber-reinforced composites. Various amounts of CNCs (1, 2, 4, and 6 wt%) were added to bisphenol A diglycidyl ether-based epoxy resin (DGEBA), and the optimum CNC loading was determined as 4 wt% in terms of mechanical and thermal properties. Compared to the reference sample containing a neat epoxy matrix with the obtained carbon fiber/CNC-epoxy (CNC/epoxy/CF) and glass fiber/CNC-epoxy (CNC/epoxy/GF) hybrid nanocomposites, significant improvements have been determined in the in-plane shear modulus and strength, and flexural modulus, respectively. The mechanical properties improvements of CNC/epoxy/CF hybrid composites are approximately 0.9% higher than the CNC/epoxy/GF hybrid composites. Additionally, the distribution of CNC in hybrid nanocomposites is also investigated by scanning and transmission electron microscopies. It is noted that the homogenous dispersion of CNCs in the epoxy matrix and their diameters varied from 10 to 100 nm are detected at higher magnification.
RELATED ARTICLES
Gergő Zsolt Marton, Fanni Balogh, Gábor Szebényi
Vol. 19., No.8., Pages 809-821, 2025
DOI: 10.3144/expresspolymlett.2025.62
Vol. 19., No.8., Pages 809-821, 2025
DOI: 10.3144/expresspolymlett.2025.62
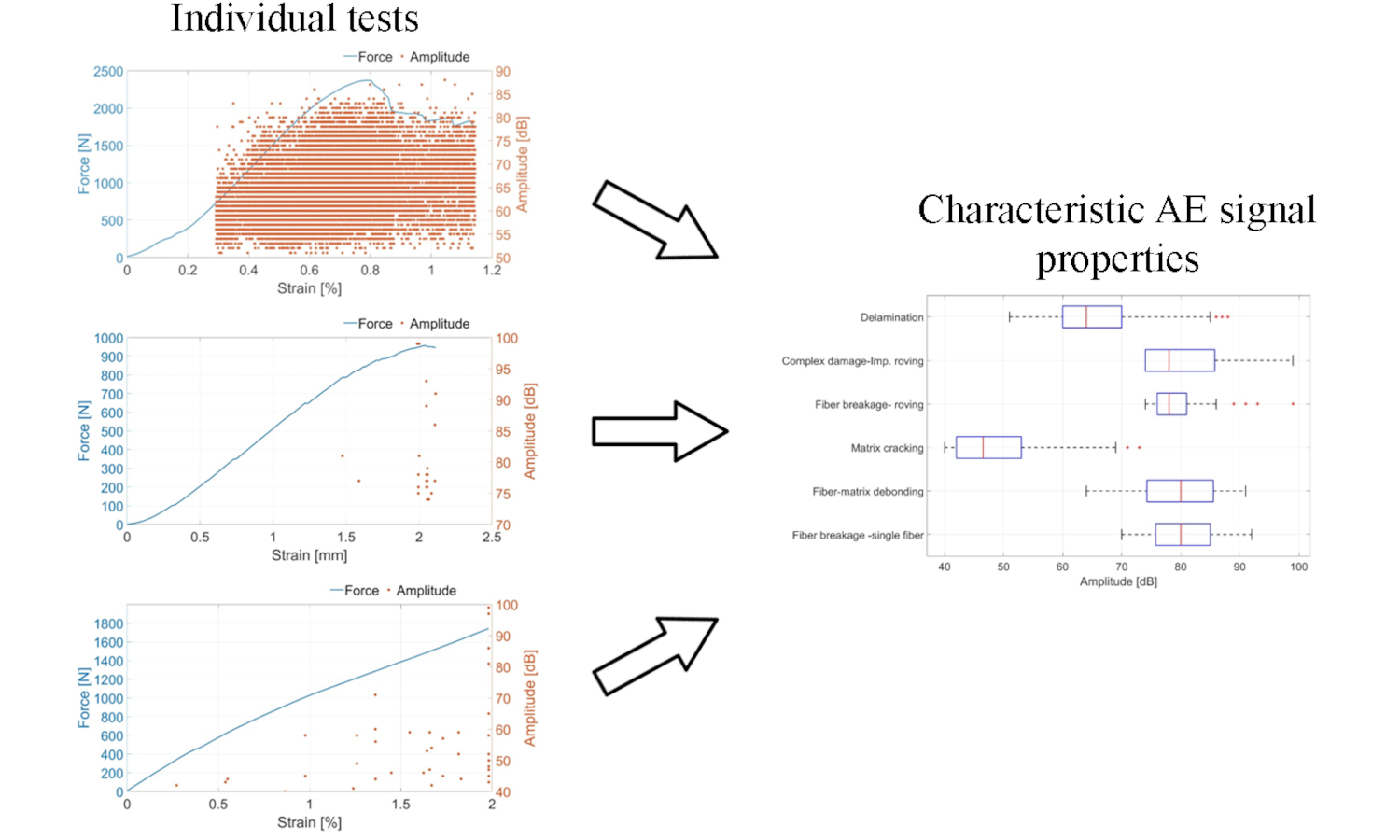
The failure of fiber-reinforced polymer composites is considered a complex process resulting from several concurrent damage mechanisms and their interactions. To better understand the damage modes of composites, which is necessary to ensure their structural health monitoring, increase their reliability, and validate different methods used for influencing their damage and failure process, it is crucial to detect, identify, and analyze different damage modes present in composite materials. The acoustic emission technique provides the opportunity to acquire damage-related data, which can be analyzed and associated with different modes of damage. In the current study, we conducted specific tests using the acoustic emission (AE) technique on the composite and its constituents, which can induce individual damage modes, thereby enabling the determination of their characteristic AE signal properties and their identification in complex composite structures.